Hot isostatic pressing of TC4 titanium alloy powder and its application
Time:2023/03/30 Pageviews:2 Share:
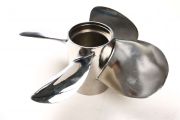
Electrode Induction Melting Gas Atomization(EIGA)
The TC4 titanium alloy is made into an electrode rod, and the electrode rod is heated and melted by an induction coil to form a fine liquid flow. After passing through the spray plate, the liquid drop is broken under the intervention of high-speed inert airflow, and quickly condenses into powder. The process uses no crucible and duct tube, and the powder which produced this way has high level of purity.
Electrode induction melting gas atomization method:
The hot isostatic pressing process uses inert gas as the energy medium and protective atmosphere, in a controlled high temperature (below 2000°C), high pressure (100-200Mpa) airtight container, applying the same static pressure from all directions to the surface of the parts or packages placed in it, therefore obtaining parts with high density, the hot isostatic pressing process has been widely used in many fields, such as the sintering and post-forming treatment of hard alloys such as TiC, and the densification of large casting pieces. Densification of target materials and printed parts, elimination of internal defects in high-temperature alloys such as titanium and molybdenum, and bonding of difficult-to-solder materials.
Illustration of hot isostatic pressing/ Hot Isostatic Pressing Internal Pore Removal Defects
The powder hot isostatic pressing (HIP) process is a method that can achieve densification and net near-shape effects at the same time. Its advantages include: High density, close to 100% relative density, good microstructure, high purity, fine grain size, uniform structure, small internal stress and other properties which can fully match or even exceed the level of forgings.
The hot isostatic pressing process of TC4 titanium alloy powder can eliminate defects and effectively improve the mechanical properties of titanium alloy pieces to meet the strict requirements of high-end equipment. At the same time, it can reduce the cost of titanium alloys, improve production efficiency and utilization of titanium alloys.
Application of Hot Isostatic Pressing Process of TC4 Titanium Alloy Powder
In 1955, the first hot isostatic pressing equipment was successfully developed in the United States, marking the birth of hot isostatic pressing technology.
At present, many powdered titanium alloy parts with excellent performance have been used in aerospace and military industries, such as aeroengines, spacecraft, hydrogen pump impellers, thin-walled cabins, air rudder skeletons, missile tails, tanks, turbine discs, submarines, etc. Periscope cylinder, etc., powdered titanium alloy will have greater development in the aviation field. In the civilian market, with the rapid growth of market demand for 3D printers, the demand for printing titanium alloy substrates is gradually increasing, and the use of TC4 titanium alloy powder for hot isostatic pressing of titanium substrates also has a strong potential market.